汽车智能表面触摸振动反馈的实现原理
近年来,随着车载人机交互技术的发展,传统的机械按键逐渐被智能化的内饰设计取代。为了提升用户的操作体验,触摸屏等智能表面越来越多地配备振动反馈功能。尽管该领域尚无统一标准,但汽车维修管理软件希望通过本文从感知原理、实现方法、振动类型、振动传递及噪声等角度探讨了触摸振动反馈的实现与评价。
触觉感知与评价
车内触摸操作主要通过指尖完成,而指尖皮肤中分布着四种主要的触觉神经元:默克尔触盘、迈斯纳小体、鲁菲民末梢和帕奇尼小体。帕奇尼小体对高频振动(200~300Hz)最为敏感,因此被称为“地震记录仪”。每个指尖大约有350个帕奇尼小体,这些小体能够感知到0.00001毫米的皮肤运动,是人类感知振动的关键信号接收器。
触觉振动反馈的设计参数
振动反馈设计的几个关键参数如下:
1. 频率:人类能够感知的振动频率范围在20~1000Hz,最敏感的频率大约在250Hz。由于振幅的变化会影响对频率的感知,因此频率变化常不被用于可靠的通讯设计。触摸振动器的选择需要根据频率特性来匹配,常用的振动器频率范围在180~350Hz之间。
2. 波形:人类对振动波形的感知较为模糊,但正弦波和方波较为容易区分。目前触摸振动反馈大多采用正弦波设计。
3. 振动时间:作为报警信号时,振动的持续时间通常为50~200毫秒;然而,触摸反馈信号的振动时间控制在30~60毫秒为最佳,超过此范围可能引发不适感。
4. 振幅:振动的振幅通常为0.1毫米左右,这是指偏离初始位置的最大位移量。振幅大小直接影响手指的感知强度,并与频率紧密相关。
5. 加速度:振动反馈的加速度一般要求超过2g,以确保足够的振动感知。单位为mm/s²或g。
振动系统的组成部分
触摸振动系统通常包括以下几个部分:
1. 活动件:如面板、皮革、织物和触摸屏等,是用户进行触摸操作的表面。这些部件在振动方向上具有一定的弹性自由度。
2. 固定件:如外壳、底座等,主要与整车结构连接,保持相对固定状态。
3. 悬架系统:利用弹片、橡胶球、泡棉等零件将活动件和固定件弹性连接,起到振动传递的作用。设计时也可通过面板局部的弹性结构来实现这一功能。
4. 振动器:如线性电机、偏心电机和电磁铁等,用于产生振动的动力源。
5. 电控系统:负责控制振动器的驱动信号,包括频率、波形、时间等参数,以实现所需的振动手感。
振动类型及工作方式
触摸振动系统主要分为两类振动方式:
1. 激励型振动:振动器安装在固定件上,通过一次性激励作用使活动件产生自由振动,满足产品的振动需求。
2. 共振型振动:振动器直接安装在活动件上,利用振动器本身的振动带动活动件一起振动,达到产品要求的反馈效果。
振动产品的设计流程
振动方式选择:根据客户的需求,确定振动曲线、振动强度以及振动噪声的要求。再根据活动件的质量、形态来选择合适的振动器和振动方式。
模态分析:在初步设计阶段,通过CAE软件进行模态分析,评估产品的固有频率、振型以及在不同方向上的振动加速度。设计要求一阶固有频率与振动器频率匹配,触摸区域的振动加速度达到设计标准,并确保振动传递效率符合要求。设计原则是以最小的振源强度满足触摸区域的反馈需求,同时避免与车身共振产生的噪音。
电控系统设计
根据振动器的选择,设计相应的电控系统。以激励器为例,MCU(微控制器)输出DAC波形信号,通过功放芯片放大信号以驱动振动器。在不同阶段,如启动、保持、制动过程中,控制振动的频率、峰值和持续时间,以实现预期的振动效果。
振动传递与噪声控制
振动的传递效率是触觉反馈设计中的关键问题。通过合理设计悬架结构,优化振动的传递路径,确保触摸区域处于振动放大区,而车身安装区域则处于振动衰减区,从而避免与车体共振导致噪音。
振动传递率公式为:
激励位移
T = ———————
激励位移
其中,频率比 λ=f/f0 以及阻尼比 ζ=R/R0 决定了振动传递的效果。若 T > 1 ,振动被放大;若 T < 1 ,振动则被衰减。共振的发生往往是因为频率比接近1,此时需提高阻尼比来控制振动的放大效应。
振动反馈的测试与调整
在实际应用中,触摸振动反馈的设计需要通过装车测试来验证。通过测量振动曲线并结合客户的主观评价,对振感进行调整。当触摸区域较大时,系统可以通过电容触摸技术识别不同区域,并根据区域不同调用相应参数驱动振动器,确保振感的一致性。
汽车维修管理软件总结
触摸振动反馈作为车载人机交互中不可或缺的一部分,不仅提升了操作的可行性和安全性,还增强了用户的交互体验。随着技术的进步,智能表面触控的应用将会更加广泛。在未来,振动反馈的实现可能会通过更加创新且低成本的方案来实现,为行业带来更多的突破。
车吉祥软件
车吉祥汽车维修管理软件免费版下载 车吉祥汽车美容管理软件免费版下载 车吉祥洗车管理软件免费版下载门店提升 与 员工培训
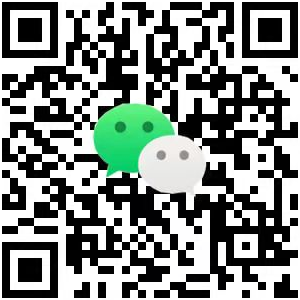
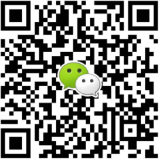
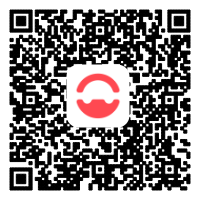